The Evolution of Metal Marking Procedures: Innovations and Applications
The realm of steel marking processes has actually seen a transformative journey marked by continuous development and adjustment to fulfill the needs of modern-day industrial methods. The applications span across a spectrum of markets, each benefiting distinctly from the advancements in steel marking procedures.
Standard Steel Stamping Techniques
Traditional metal marking strategies have long been the foundation of making processes in various sectors due to their effectiveness and accuracy. The process entails developing a steel sheet or coil into a preferred form by pushing it in between a die and a strike. This method is extensively used for producing large quantities of parts with high precision at a quick rate.
One of the crucial benefits of traditional steel marking strategies is the ability to preserve tight tolerances, making certain that each component meets the called for specs continually. This level of accuracy is necessary in sectors such as auto, aerospace, and electronic devices, where also small variances can bring about considerable problems.
Furthermore, traditional metal stamping methods supply affordable options for mass production contrasted to various other producing techniques. The capability to stamp parts in fast sequence decreases production time and minimizes labor costs, making it an attractive choice for businesses seeking to maximize their production procedures.
Appearance of High-Speed Stamping
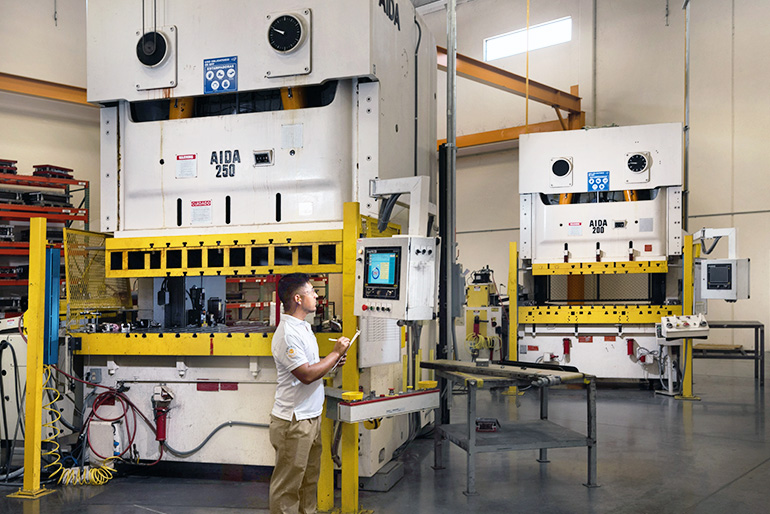
Among the key advantages of high-speed marking is its capability to preserve precision and consistency also at accelerated processing rates. This accuracy is crucial in sectors where tight resistances and elaborate styles are called for. Additionally, high-speed stamping permits the processing of a wide variety of products, consisting of light weight aluminum, stainless steel, and copper, further expanding its applicability across various industries.
Moreover, the appearance of high-speed stamping has made it possible for producers to fulfill the expanding need for complex components in markets such as auto, aerospace, and electronic devices (Metal Stamping). By leveraging the speed and accuracy of high-speed stamping technology, companies can boost their competition in a swiftly developing market landscape
Advancements in Tooling Innovation
With the development of high-speed stamping making it possible for enhanced precision and efficiency in metal forming processes, the area of metal marking has seen substantial innovations in tooling modern technology. Tooling technology plays a critical duty in steel stamping operations, influencing aspects such as product high quality, manufacturing rate, and general important link cost-effectiveness.
Additionally, developments in products science have led to the development of tooling products with boosted durability, use resistance, and thermal conductivity. By using these innovative materials, tooling suppliers can produce passes away and molds that endure the high pressures and temperature levels involved in steel stamping processes, causing longer device life and better manufacturing effectiveness. Additionally, technologies in device layout, such as using simulation software application and additive production methods, have made it possible for the development of complex tooling geometries that were previously challenging to generate. Overall, these improvements in tooling check it out modern technology have changed the metal stamping market, enabling suppliers to accomplish higher degrees of accuracy, efficiency, and expense savings.
Combination of Automation in Stamping
As automation proceeds to reshape the landscape of steel stamping procedures, the combination of automated systems has actually come to be increasingly prevalent in modern manufacturing centers. Automated systems provide numerous benefits in metal marking, including enhanced efficiency, boosted accuracy, and improved safety and security. By including automation right into marking procedures, producers can decrease cycle times, reduce product waste, and enhance production throughput.
One of the crucial parts of automation in stamping is making use of robot arms for tasks such as product handling, part manipulation, and high quality examination (Metal Stamping). These robot systems can execute recurring and labor-intensive jobs with speed and accuracy, releasing up human operators to concentrate on more complex operations. Furthermore, automation enables for real-time monitoring and change of marking processes, resulting in greater general procedure control and top quality guarantee
Furthermore, the integration of automation in marking enables suppliers to attain regular component high quality, meet limited resistances, and improve overall productivity. As modern technology you could try here remains to advancement, the duty of automation in metal stamping processes is expected to expand additionally, driving technology and performance in the manufacturing market.
Applications Across Diverse Industries
Including metal marking procedures across varied sectors showcases the versatility and flexibility of this manufacturing method. In addition, the appliance market advantages from metal marking procedures to make components for fridges, cleaning equipments, and other house home appliances. The adaptability of steel stamping processes makes it a beneficial manufacturing method across various markets, demonstrating its relevance in modern manufacturing procedures.
Final Thought
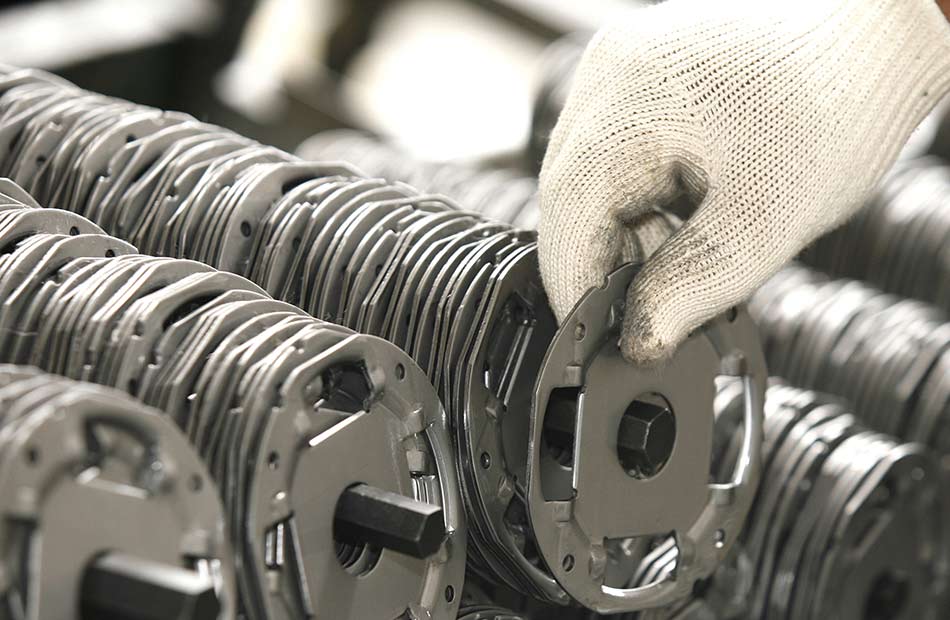